As a professional supplier, sinoder and its partner has manufactured and built tens of different coal gasfication plants in China and Oversea Since 2000. Now we pay much attention to the international market. We supply single stage or double stage gasification plant with diameter from Ø 0.8- Ø3.6m based on the actual requirement from different customers.
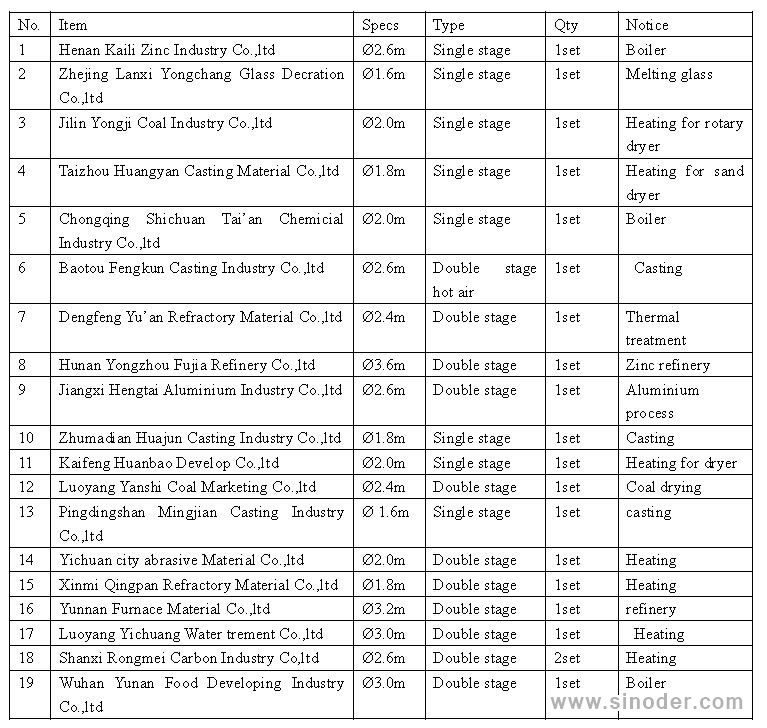
The producer gas is assorted in three kinds according to different gas agent.
A. Air gas(using air as agent).
B. Water gas(using steam as agent).
C. Mixed gas(using air and steam as agent).
Coal gasification theory
Basic chemical reaction Producer gas is made by the gasification agent, which is mixture of steam and air, goes through red-hot fixed burning bed. The oxygen and steam content in the air react with the carbon in the fuel, generate the producer gas with ingredients like CO, CO2, H2, CH4, C2H4, N2 etc.
Reaction of steam and carbon is endothermic reaction: C + H2O= CO + H2
When oxygen and carbon react, then heat output: 2C + O2 =2CO
Reaction of carbon monoxide and steam: CO + H2O = CO2 + H2
Some steam here reacts with carbon monoxide. When every volume of carbon monoxide translates into carbon dioxide, generates the same volume of hydrogen at the same time. In the reducing zone, quick reaction is occurred when the temperature is below 1200 Celsius degree . CO2 + C = 2CO and H2O + C=H2 + CO
When the coal gas goes through the reducing zone, flammable gas content rises rapidly, carbon dioxide and steam content decrease. Across the reducing zone, a part of coal gas is exported, flows through bottom cyclone and wind cooler, this part of gas is called “downstage coal gas”, its temperature is around 400-550 Celsius degree.
In the carbonation stage, the coals added in the gasifier are dried, preheated and carbonated, generate steam, tar and coal gas, exported from the top of gasifier together, this part of gas is called “up-stage coal gas”, its temperature is around 100-150 Celsius degree.
Hot gas process flow chart
Put the 40~60mm coal into the coal bin by the lifting equipment, and then the program controlled coal feeder charging the coal into the double stage gasifier . The air blower blowing the mixed air and steam as the gasification agent, from the air and steam mix chamber at the bottom of the gasifier.
The gasification agent reacted with 1200°Ctemperature semicoke at the gasifying section of the gasifier,
and generated the combustible gas.The component of the gas is CO is about 31~33%, H2 is about 9~10%, CH4 is about 0.4%~0.5% meanwhile at the carbonize section of the gasifier,
utilize the waste heat of the down stage gas make the carbonizing to generate CO is about 29~31%.H2 is about 17~19%
CH4 is about 1~3%, CnHm is about 0.2~0.4% combustible gas.The coal gas temperature of the carbonization section is around 100~150C,
the gas flow through the electric detarrer to get rid of the dust and tar,and then flow into the gas main. The water and tar gathered from the bottom of the detarrer was sending to the tar tank.
The coal gas temperature of the gasifying section is around 550~600°C,
flow through the cyclone dust catcher to removing the big granular dust, and then flow into the gas main.
The two stage gas was combined at the gas main, and its temperature is around 150~250C. The hot gas removing tar technology takes full advantage of the sensible heat of the gas.And it is a good choice for there is less demanding for the gas cleanness requirement.
Application
Machinery Industry:high manganese steel quenching furnace,annealing furnace,forging furnace,tempering furnace,etc.
Non-ferrous metal industry:copper melting furnace,aluminum melting furnace,etc.
Building materials industry:building ceramics,sanitary ceramics,etc.
Silicate industry:glass,grinding wheel,refractory materials,etc.
Boiler:all kinds of boilers using producer gas as the fuel.
Chemical industry:drying and calcination in chemical products.
Nonmetal industry:mine materials drying and calcination.
Planting industry:vegetable and flower greenhouses warming.
Food industry:food dehydration and drying.
Advantage:
1.5Kg standard coal in it=1.1Kg diesel=12KWh.
cost 70% lower than electric furnace,60% lower than oil furnace,30% lower than coal furnace.
Performance:
Easy operation as electric and oil furnace.
Full automatical electric control,precisely temperature control.
Continuous automatic slag removal,stable gas production and easy operation.
Clean and green.
SINODER Coal Gasifier Plant for Mine Calcination in Working Video
SINODER Coal Gasifier System + Rotary Kiln Calcination Plant